The Innovative World of Plastic Mold Injection
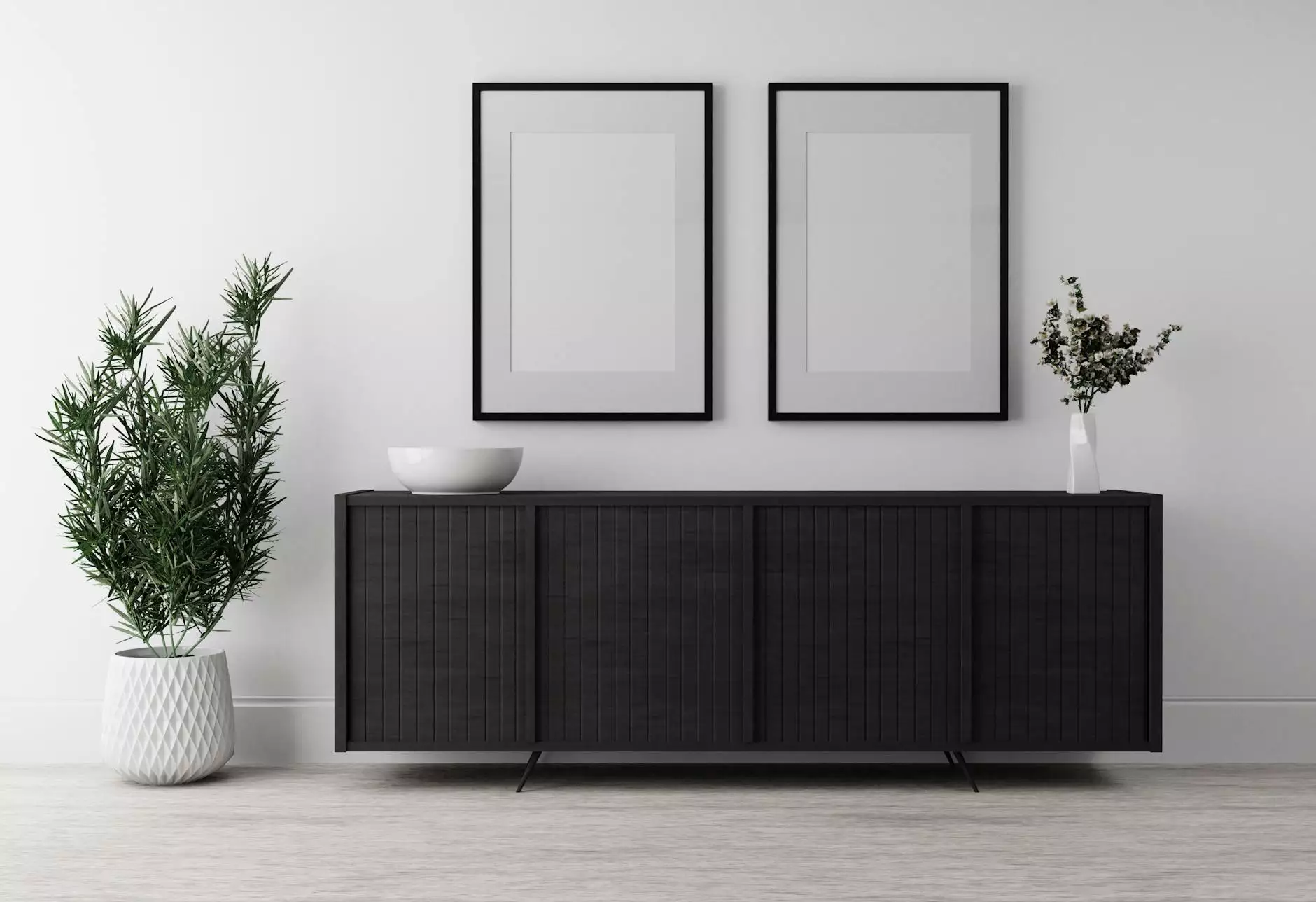
In the modern manufacturing landscape, few processes can boast the efficiency, versatility, and precision found in plastic mold injection. This method has become a cornerstone of production across various industries, including automotive, electronics, and consumer goods. At deepmould.net, we delve deep into the intricacies of this technology, exploring its advantages, applications, and future potential in the realm of metal fabrication.
Understanding Plastic Mold Injection
Plastic mold injection is a manufacturing process whereby molten plastic is injected into a mold to create a specific part or component. This method allows for the production of complex shapes with exceptional accuracy and repeatability. The process involves several critical steps:
- Material Selection: The choice of plastic material is crucial and can range from thermoplastics to thermosetting plastics.
- Heating: The selected plastic is heated until it reaches a molten state, optimizing it for injection.
- Injection: The molten plastic is injected into the mold cavity under high pressure.
- Cooling: Once the mold is filled, it cools and solidifies the plastic into the desired shape.
- Demolding: After cooling, the mold is opened, and the finished product is ejected.
Advantages of Plastic Mold Injection
The popularity of plastic mold injection can be attributed to a myriad of advantages it offers over traditional manufacturing methods:
- Efficiency: The speed of production is unmatched, allowing for high-volume manufacturing.
- Design Flexibility: Designers can create intricate shapes and detailed designs that would be difficult or impossible to achieve with other methods.
- Cost-Effectiveness: While initial setup costs may be high, the ability to produce large quantities quickly drives down the cost per unit.
- Material Variety: A wide range of plastic materials can be used, catering to different performance specifications and application needs.
- Reduced Waste: The process generates less scrap material compared to other fabrication processes.
Applications of Plastic Mold Injection in Metal Fabrication
In the realm of metal fabrication, plastic mold injection serves as an invaluable complement to traditional techniques. Consider how this technology integrates with metal fabrication:
1. Automotive Industry
In the automotive sector, components such as dashboards, panels, and housings are increasingly manufactured using plastic mold injection. This allows for:
- Reduction of weight, enhancing fuel efficiency.
- Increased design flexibility, accommodating contemporary aesthetic trends.
- Quieter operation due to the absorption of vibrations.
2. Consumer Electronics
In consumer electronics, plastic mold injection has transformed the way products like smartphones, tablets, and laptops are produced. Key advantages include:
- The ability to create complex housings that snap fit together seamlessly.
- Robustness and protection for sensitive electronic components.
- Lightweight designs improving portability for end users.
3. Medical Devices
The medical industry demands high precision and sterility, making plastic mold injection a preferred method for manufacturing medical devices and components. Benefits include:
- Customization to specific medical applications, enhancing product effectiveness.
- Adherence to strict regulatory standards ensuring safety and efficacy.
- Cost-effective production of single-use items, reducing the risk of contamination.
Challenges and Considerations in Plastic Mold Injection
While plastic mold injection offers numerous advantages, it does come with its own set of challenges:
1. High Initial Costs
The cost of designing and manufacturing molds can be significant, which poses a barrier for small-scale producers. However, these costs must be weighed against the long-term savings achieved through high-volume production.
2. Material Limitations
Not all plastics are suitable for plastic mold injection, as some materials may not flow well or may not achieve the desired finish or properties.
3. Environmental Concerns
The environmental impact of plastic production is a growing concern. Manufacturers are pushed to innovate and seek sustainable materials that fulfill eco-friendly standards.
Future Trends in Plastic Mold Injection
As the industry continues to evolve, several trends are emerging in the field of plastic mold injection:
1. Automation and Smart Manufacturing
The integration of automation and AI technologies is streamlining the production process. Smart factories are utilizing IoT (Internet of Things) devices to monitor production efficiency and predict maintenance needs.
2. Advances in Material Science
Continued research in material science is leading to the development of new plastics that are stronger, lighter, and more sustainable. Biodegradable and recycled plastics are becoming increasingly popular, aligning with green manufacturing goals.
3. Customized Producing
The demand for personalized products is on the rise. Plastic mold injection technology is evolving to meet these consumer demands by enabling shorter production runs and faster turnaround times for customized designs.
Conclusion
In conclusion, the world of plastic mold injection is one of immense potential and growth. As industries continue to embrace this manufacturing method, understanding its benefits, applications, and future trends is essential for professionals engaged in metal fabrication and related fields. At deepmould.net, we are dedicated to exploring the cutting-edge practices and innovations that are shaping the future of manufacturing, ensuring you remain at the forefront of industry advancements.
Whether you're an established business or a budding entrepreneur, recognizing the advantages of plastic mold injection can significantly enhance your production capabilities, unlock new market opportunities, and elevate your competitive edge in today’s dynamic market.