CNC Machining Parts & Their Essential Role in Metal Fabrication
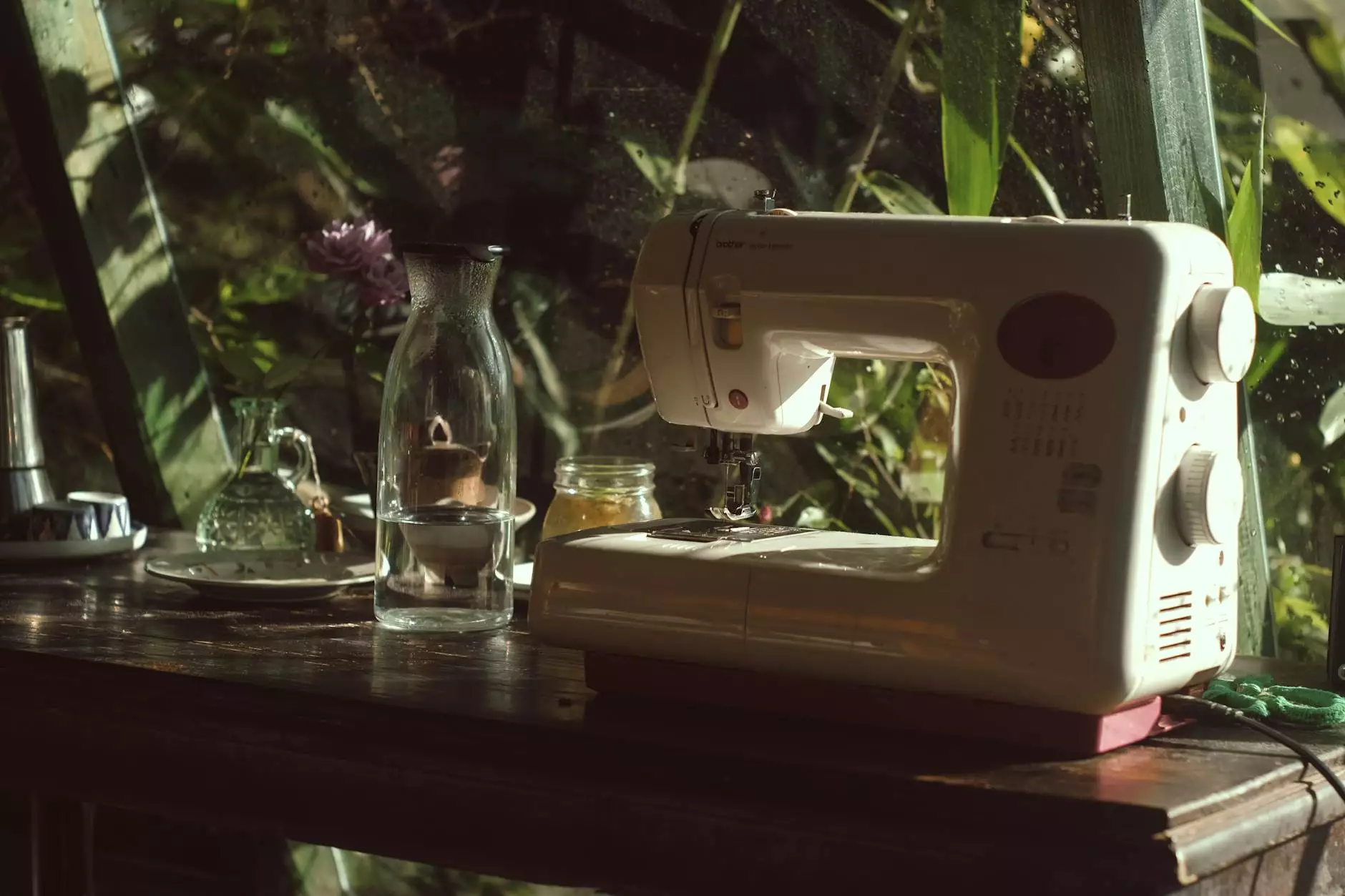
CNC machining parts play a crucial role in the world of manufacturing, particularly in the metal fabrication industry. As industry standards rise, so does the need for precision-engineered components. This article delves deep into the significance of CNC machining parts, their applications, benefits, and what to consider when selecting a reliable manufacturer like DeepMould.net.
Understanding CNC Machining
CNC, or Computer Numerical Control, refers to the automation of machine tools via computers executing pre-programmed sequences. This process allows for incredible precision and repeatability, making it a favored manufacturing method for producing machining parts.
Key Components of CNC Machining
- CNC Machine: The primary equipment that performs various operations, including milling, turning, and drilling.
- Control Software: Programs that enable the operator to control the machinery and optimize the machining processes.
- Workpiece Material: The metal or composite material being machined, which is often custom-specified.
- Cutting Tools: Specialized tools that physically remove material from the workpiece to create the desired shape.
The Importance of CNC Machining Parts
In today’s competitive market, the significance of cnc machining parts cannot be overstated. Here are several reasons why they are indispensable:
1. Precision and Accuracy
One of the standout features of CNC machining is its capability to produce parts with extreme precision. This level of accuracy minimizes waste and maximizes efficiency, leading to superior quality products. Manufacturers can achieve tolerances as tight as ±0.001 inches, which is essential for industries that require strict adherence to specifications.
2. Versatility
CNC machining can handle a variety of materials, including aluminum, steel, titanium, and plastics, making it incredibly versatile. This adaptability means that businesses can use CNC technology to produce a vast array of components, from small precision parts to large aerospace components.
3. Scalability
Whether you need a single prototype or hundreds of production parts, CNC machining easily adapts to different order volumes. This scalability is vital for businesses looking to expand their market share without compromising on quality.
4. Cost-Effectiveness
While the initial investment for CNC machinery might be significant, the long-term cost savings are impressive. Due to the efficiency of CNC processes, businesses can reduce labor costs, minimize material wastage, and improve production speeds. Over time, these savings can be substantial.
5. Complex Geometries
CNC machining allows manufacturers to create intricate designs that would be impossible or prohibitively expensive to produce with traditional machining methods. This capability is particularly important in industries such as aerospace and medical devices, where complex geometries are often required.
Applications of CNC Machining Parts
CNC machining parts are used in a wide variety of industries. Some of the most common applications include:
Aerospace Industry
The aerospace sector requires components that are not only lightweight but also incredibly strong. CNC machining is used to manufacture critical parts such as brackets, fittings, and various structural components. The precision of cnc machining parts is vital in ensuring safety and compliance with stringent regulations.
Automotive Industry
In automotive manufacturing, CNC machining is employed to produce engine components, transmission parts, and chassis elements. The ability to quickly produce high-quality parts is essential for keeping up with the demands of modern automotive production lines.
Medical Devices
Medtech requires the utmost precision as the components must fit together seamlessly and be reliable in critical applications. CNC machining provides the accuracy necessary to produce surgical instruments, implants, and other medical devices that meet FDA regulations.
Consumer Electronics
With the rise of technological advancement, consumer electronics industries rely on CNC machining for manufacturing components like frames, chassis, and internal mechanisms that demand precise dimensions and high throughput.
Industrial Equipment
Heavy machinery and industrial equipment manufacturers utilize CNC machining for components that require robust construction yet precise dimensions, like gears, housings, and support structures.
Choosing the Right Manufacturer for CNC Machining Parts
Selecting the right partner for CNC machining is crucial for the success of your projects. Here are key factors to consider:
1. Experience and Expertise
Look for companies with a proven track record in the industry. They should have experience in machining the specific materials associated with your project and knowledge of the latest technologies.
2. Equipment and Technology
The quality of the machining parts greatly depends on the machinery being used. Ensure the manufacturer employs state-of-the-art CNC machines and technologies, as this will directly impact the precision and quality of your components.
3. Quality Control
Reliable manufacturers will have strict quality control protocols in place. Ask about their quality assurance processes and certifications. A commitment to quality should be evident in their operations.
4. Customer Service
Excellent communication is essential in any business relationship. Choose a manufacturer that values customer service and is willing to collaborate with you throughout the manufacturing process.
5. Competitive Pricing
While cost should not be the only consideration, it is an important factor. Obtain quotes from multiple manufacturers and compare, but be wary of prices that seem too good to be true, as they may indicate a compromise in quality.
The Future of CNC Machining Parts
The future of cnc machining parts looks promising. As technology evolves, we can expect to see enhancements such as:
- Automation: Increased automation in CNC machining will improve efficiency and reduce production costs.
- Advanced Materials: Development of new materials tailored for CNC machining will expand the capabilities and applications of this technology.
- Integration with IoT: Smart manufacturing through Internet of Things (IoT) technology will enable real-time monitoring and optimization of CNC machining processes.
Conclusion
Understanding the vital role of cnc machining parts in the metal fabrication industry is essential for any business looking to thrive in a competitive landscape. By leveraging the power of CNC machining, companies can achieve unparalleled precision, versatility, and cost-effectiveness. When choosing a manufacturer, consider factors such as experience, technology, and customer service to ensure the best outcome for your projects. Partnering with a reliable manufacturer like DeepMould.net can set your business on the path to success, enabling you to meet the demands of your industry head-on.