The Rise of Quality Lathe Parts Made in China
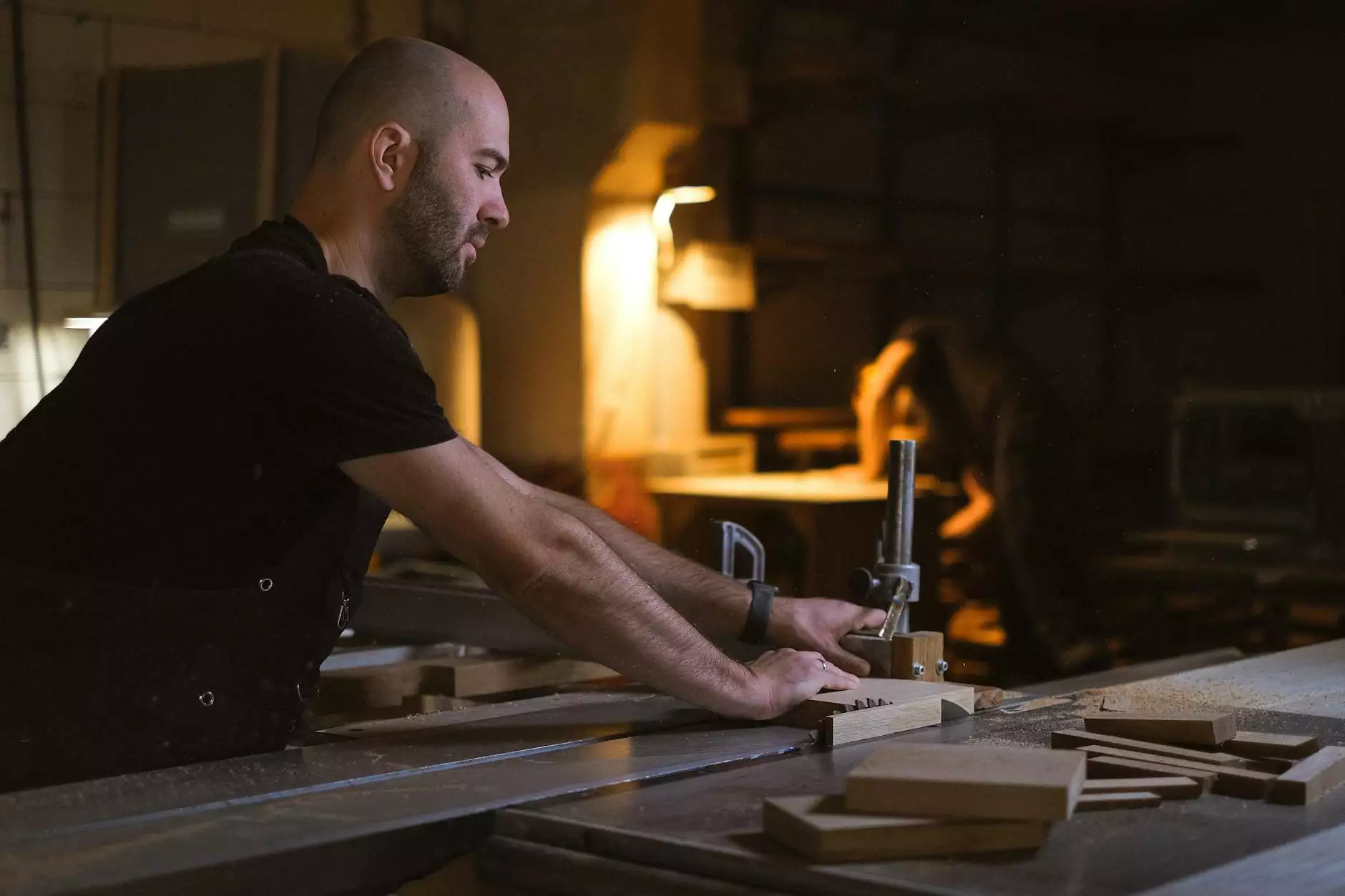
The manufacturing landscape has dramatically evolved over the past few decades, especially in countries like China. Lathe parts made in China have emerged as a pivotal component in various industries, especially among metal fabricators. With an unparalleled blend of quality, innovation, and affordability, Chinese manufacturers have solidified their reputation on the global stage. This article delves into the various aspects of lathe parts production in China, highlighting their benefits, trends, and what to keep in mind when sourcing such products.
Understanding Lathe Parts
Lathe parts are essential components in metalworking, used extensively in industries like automotive, aerospace, and machinery manufacturing. Lathe machines are designed to shape metal and other materials by removing material using a rotating workpiece and a stationary cutting tool. The precision and quality of the parts produced can determine the overall performance and longevity of the end product.
Types of Lathe Parts Manufactured in China
China is known for producing a vast array of lathe parts, catering to different needs and specifications. Some of the commonly manufactured lathe parts include:
- Spindles: Critical for the rotation of the workpiece.
- Chuck Bodies: Essential for securing materials during machining.
- Tool Holders: Used to hold cutting tools at precise angles.
- Carriers: Designed to hold multiple tools or workpieces.
- Back Plates: Provide support and stability for the working assembly.
Benefits of Sourcing Lathe Parts Made in China
The choice to source lathe parts made in China offers numerous advantages that are hard to overlook. Here are some key benefits:
- Cost-Effectiveness: Due to lower labor costs and efficient production processes, Chinese manufacturers typically offer competitive pricing.
- High Quality: Many Chinese factories employ advanced technologies and stringent quality control measures, ensuring that products meet international standards.
- Variety and Innovation: The wide range of products and continuous innovation allow buyers to find specific solutions tailored to their needs.
- Scalability: Manufacturers can quickly ramp up production according to the demand, which is particularly beneficial for businesses looking to scale operations.
- Strong Supply Chain: China has a robust supply chain infrastructure, ensuring timely delivery of raw materials and finished products.
The Manufacturing Process of Lathe Parts Made in China
Understanding the manufacturing process of lathe parts made in China can provide insights into their quality and reliability. Below is a comprehensive overview of the typical production stages:
1. Design and Prototyping
The production process begins with design and prototyping, where engineers create detailed specifications. Advanced computer-aided design (CAD) software helps in the precise mapping of the lathe parts.
2. Material Selection
Choosing the right materials is crucial. Common materials used for lathe parts include:
- Steel
- Aluminum
- Stainless Steel
- Plastic Composites
3. Machining Processes
After material selection, the machining processes begin, which may include:
- Turning: The primary method used for machining lathe parts.
- Milling: Used for more complex shapes and surfaces.
- Drilling: To create holes and attachments.
4. Quality Control
Quality control is checked at various stages to ensure that all products meet the desired standards. This may include dimensional checks, material inspections, and performance tests.
5. Finishing
After machining, lathe parts typically undergo finishing processes such as:
- Coating: For rust prevention and enhanced aesthetic appeal.
- Polishing: To improve surface finish and reduce friction.
6. Packaging and Shipping
Finally, products are packaged securely to prevent damage during transit. Efficient logistics and shipping channels ensure prompt delivery to customers worldwide.
Choosing the Right Supplier for Lathe Parts Made in China
Finding the right supplier is crucial for ensuring the quality and reliability of your lathe parts. Here are some tips on how to select a trustworthy manufacturer:
1. Research and Compare
Conduct thorough research on potential suppliers. Look for reviews, ratings, and testimonials from previous customers. Platforms like Alibaba or Made-in-China can be great resources for initial research.
2. Request Samples
Before making a bulk order, request samples to evaluate quality and craftsmanship. This step can help mitigate risks associated with large investments.
3. Evaluate Certifications
Check for certifications such as ISO 9001, which indicates a commitment to quality management. Additionally, certifications related to specific industries may also be important.
4. Communication
Effective communication is vital. Choose a supplier that is responsive and transparent about their processes and capabilities. This can be a key determinant of a successful partnership.
5. Assess Delivery Times
Understand the supplier’s lead times and shipping methods to ensure they align with your project timelines. Reliable suppliers can often provide accurate delivery estimates.
Trends in the Manufacturing of Lathe Parts Made in China
The manufacturing industry in China continuously evolves, driven by technological advancements and market demands. Here are some ongoing trends that are influencing the production of lathe parts made in China:
1. Automation and Industry 4.0
More manufacturers are adopting automated production processes, leading to increased efficiency and reduced human error. Industry 4.0 practices enable real-time data communication, optimizing manufacturing workflows.
2. Use of Advanced Materials
There is a growing trend toward the usage of advanced materials that enhance durability and performance. Manufacturers are exploring carbon fiber and other high-performance materials for specific applications.
3. Sustainable Practices
With increasing environmental concerns, many manufacturers are adopting sustainable practices. This includes the use of eco-friendly materials, energy-efficient production methods, and waste reduction strategies.
4. Customized Solutions
The demand for customized lathe parts is rising as industries seek tailored solutions for their unique challenges. Manufacturers are leveraging flexibility in production to meet these needs.
The Future of Lathe Parts Made in China
The future looks promising for the landscape of lathe parts made in China. As technology continues to advance and global markets evolve, Chinese manufacturers are likely to maintain their position as leaders in metal fabrication. Businesses looking for high-quality, cost-effective solutions will continue to benefit from sourcing parts from this region.
Moreover, as the industry shifts towards more sustainable and innovative practices, suppliers who embrace these changes are expected to thrive, fostering long-term relationships within global supply chains.
Conclusion
In conclusion, the sector of lathe parts made in China offers substantial advantages for metal fabricators around the world. With a commitment to quality, affordability, and innovation, Chinese manufacturers are well-positioned to meet rapid industrial demands. By understanding the manufacturing processes, choosing the right suppliers, and keeping abreast of industry trends, businesses can successfully navigate the global manufacturing landscape and leverage the benefits it has to offer.
If you want to explore more about what deepmould.net has to offer, or if you need assistance in sourcing quality metal parts, feel free to reach out. We’re here to support your manufacturing needs!