Precision Plastic Injection: Revolutionizing Metal Fabrication
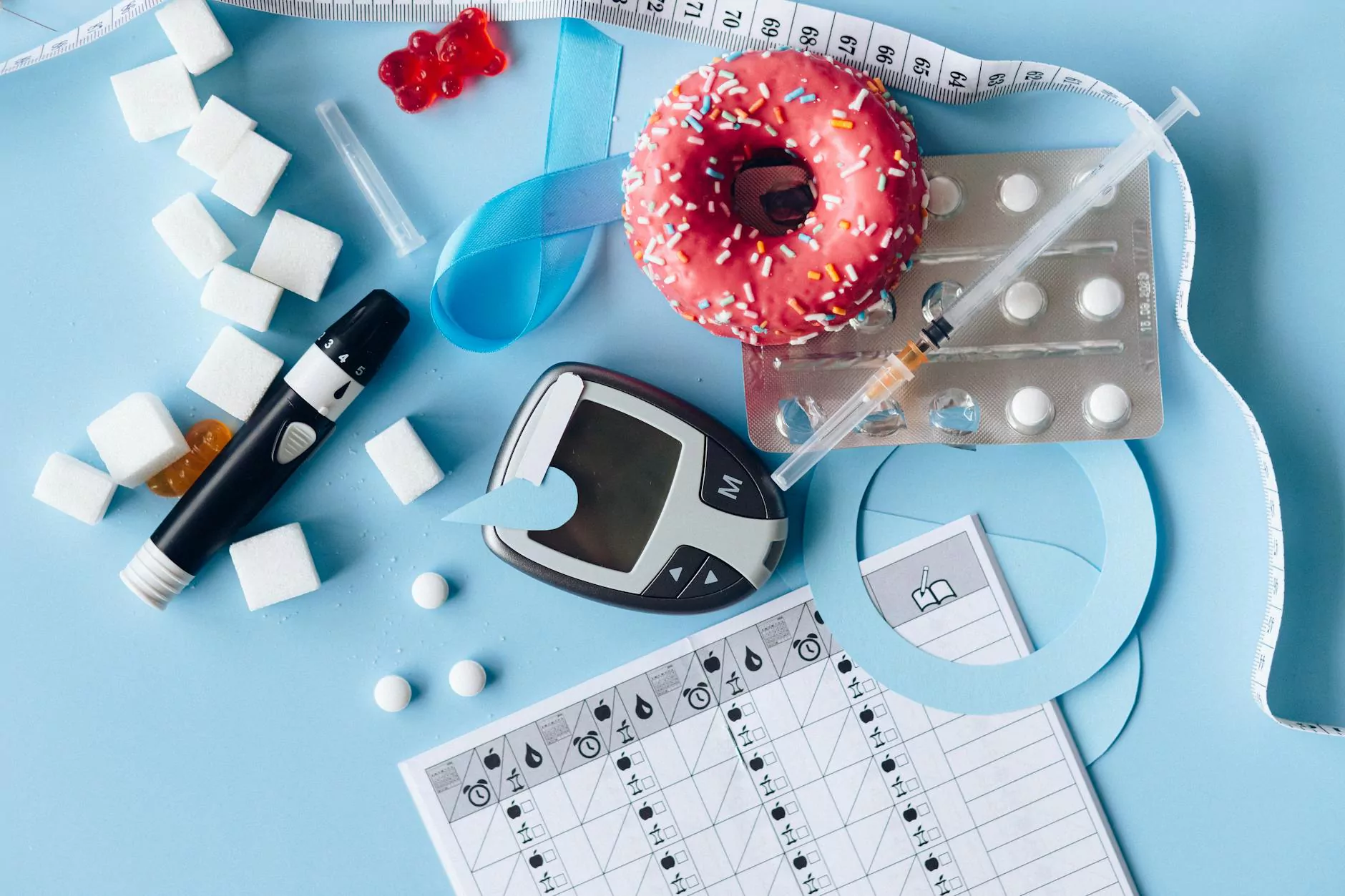
In the realm of modern manufacturing, precision plastic injection stands out as a groundbreaking technique that is reshaping the landscape of production. This article delves into the intricacies of this remarkable technology, its impact on metal fabrication, and why businesses should consider adopting it for their manufacturing processes.
Understanding Precision Plastic Injection
Precision plastic injection is a manufacturing process that involves injecting molten plastic into a mold to create precise plastic parts. The process is celebrated for its ability to produce complex shapes and designs with exceptional accuracy, making it a vital choice for industries ranging from automotive to medical devices.
The Process of Precision Plastic Injection
The precision plastic injection process can be broken down into several key steps:
- Material Selection: The quality of plastic materials used is paramount. Engineers select thermoplastics or thermosetting plastics based on the desired properties of the final product.
- Mold Design: Crafting an optimal mold is crucial. Computer-aided design (CAD) software enables engineers to create intricate and functional mold designs that accommodate specific product requirements.
- Injection: Once materials and molds are prepared, molten plastic is injected at high pressure into the mold cavity, allowing it to take the desired shape.
- Cooling: The injected plastic cools and solidifies, ensuring that it retains the exact shape and characteristics of the mold.
- Demolding: The new plastic part is carefully removed from the mold, ready for further processing, such as finishing or assembly.
Advantages of Precision Plastic Injection
The adoption of precision plastic injection offers numerous advantages to businesses involved in metal fabrication:
1. High Precision and Accuracy
One of the most significant benefits of this technology is its ability to produce highly precise components. The fine control over the injection process ensures that tolerances are kept to a minimum, resulting in parts that fit and function exactly as intended.
2. Enhanced Speed and Efficiency
With the ability to produce large quantities of parts quickly, precision plastic injection reduces production time significantly. This efficiency allows companies to meet tight deadlines and respond rapidly to market demands.
3. Cost-effectiveness
While the initial setup costs for molds can be high, the long-term savings associated with reduced labor, speed of production, and minimal waste make precision plastic injection a cost-effective solution for many manufacturers.
4. Versatility in Design
Precision plastic injection is not limited to simple shapes. Engineers can produce complex geometries, undercuts, and intricate designs that would be challenging or impossible with traditional metal fabrication methods.
5. Material Variety
A wide range of plastics can be used in the injection molding process, allowing manufacturers to choose materials that best suit their specific needs, such as thermal stability, chemical resistance, or aesthetic qualities.
Applications of Precision Plastic Injection in Metal Fabrication
The integration of precision plastic injection into metal fabrication processes opens new doors for innovation. Here are some key applications:
1. Automotive Industry
Precision plastic parts are increasingly utilized in automotive manufacturing. Components such as dashboards, panels, and even intricate wiring harness casings benefit from the advantages of injection molding.
2. Medical Devices
The medical field demands the highest standards of precision and hygiene. Precision plastic injection facilitates the production of components such as syringes, surgical instruments, and disposable PPE with utmost accuracy and compliance with regulatory standards.
3. Electronics
As electronics become smaller and more complex, the need for precise and lightweight components has surged. The electronics industry utilizes precision plastic injection for housings, enclosures, and connectors that require exact specifications.
4. Consumer Products
The consumer goods market benefits immensely from precision plastic injection. From toys to kitchen appliances, the technology allows for creative designs that attract customers while ensuring functionality.
5. Aeronautics and Defense
In the aerospace sector, where weight reduction is critical, precision plastic components are used in cabin fittings, interior components, and housings for specific electronic devices.
Challenges and Solutions in Precision Plastic Injection
While precision plastic injection offers many benefits, manufacturers may face challenges. Understanding these challenges and their solutions is essential for successful implementation.
1. Initial Investment Costs
The initial costs associated with molds and machinery can be substantial. However, these costs can be mitigated through careful planning, choosing the right materials, and negotiating with suppliers for better mold pricing.
2. Potential for Defects
Defects such as warping or incomplete filling can occur if the process is not correctly monitored. Implementing precise controls and utilizing advanced technologies such as simulation software can help minimize these risks.
3. Maintenance of Equipment
Regular maintenance of injection machinery is crucial for sustaining quality and efficiency. Establishing a robust maintenance schedule can prevent unforeseen breakdowns and maintain productivity.
The Future of Precision Plastic Injection
The future of precision plastic injection looks promising, with exciting developments on the horizon. With the increasing demand for sustainability, manufacturers are exploring bio-based and recycled materials. Additionally, as automation and smart manufacturing continue to evolve, the integration of AI and machine learning into the injection molding process will enable even greater precision, efficiency, and adaptability.
Conclusion
In conclusion, precision plastic injection is more than just a manufacturing process; it is a technology that is redefining efficiency, precision, and versatility in the metal fabrication industry. As businesses continue to seek innovative solutions to meet consumer demands, adopting this cutting-edge technique can pave the way for sustained growth and competitiveness. Embracing the future of manufacturing starts with understanding and implementing the principles of precision plastic injection, an investment that promises substantial returns in productivity and quality.
For businesses looking to enhance their manufacturing capabilities, consider exploring how DeepMould can assist with your precision plastic injection needs. Unlock the potential of your production line today!